Understanding GRP: The Future of Composite Materials
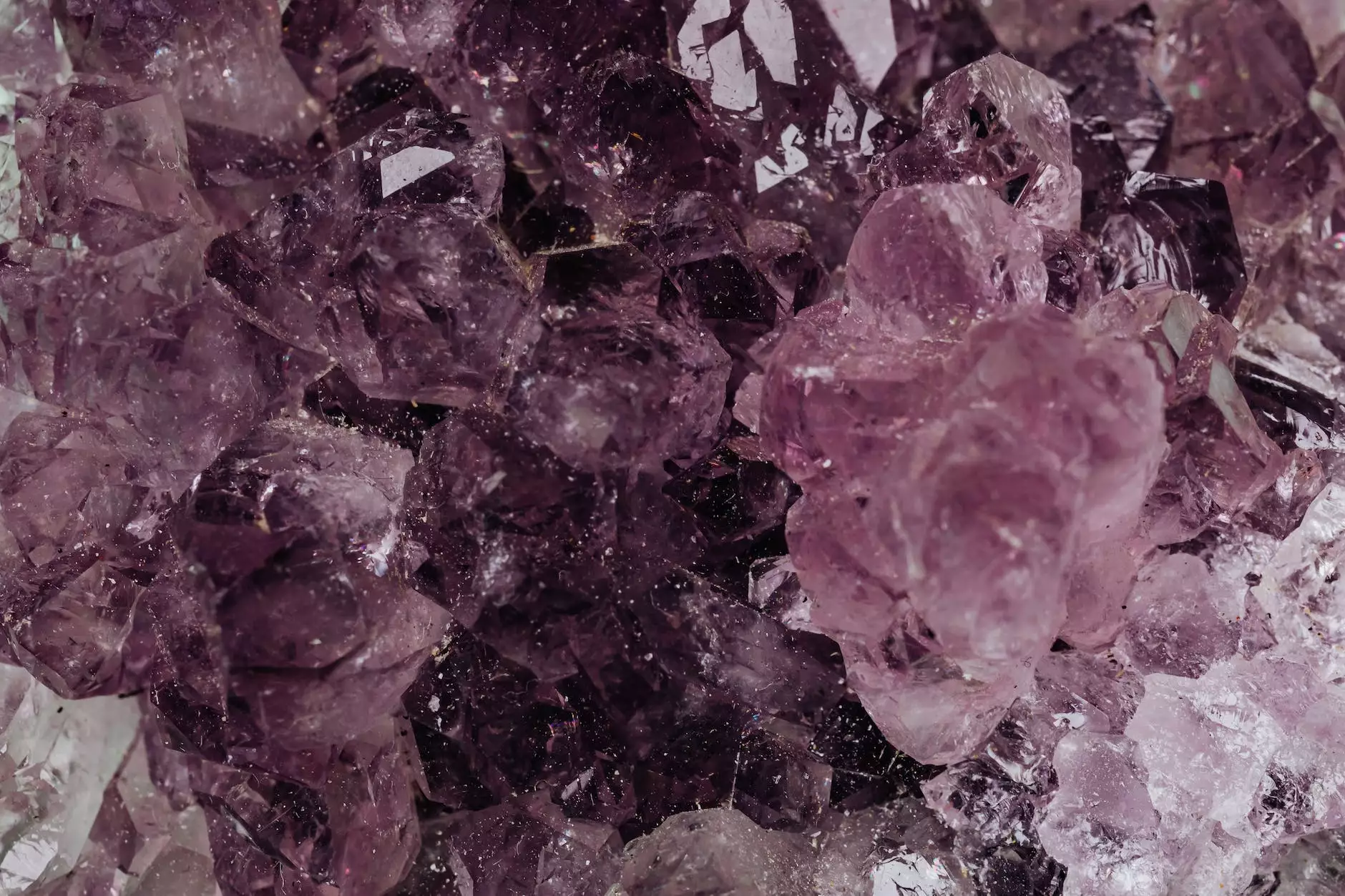
Glass Reinforced Plastic (GRP) is transforming the landscape of manufacturing and construction, becoming an essential material in various industries. Its versatility, lightweight characteristics, and strength make it an ideal choice for an array of applications. In this comprehensive article, we will explore what GRP is, its advantages, applications, and why Celtic Composites is a leader in this space.
What is GRP?
GRP, or Glass Reinforced Plastic, also known as fiberglass reinforced plastic, is a composite material made of a polymer matrix reinforced with glass fibers. This combination produces a material that is both strong and lightweight, offering a remarkable strength-to-weight ratio that is favorable in many applications.
The Composition of GRP
The typical structure of GRP consists of:
- Matrix Resin: Usually polyester, epoxy, or vinyl ester, the resin binds the fibers together and provides chemical resistance.
- Glass Fibers: These are the reinforcing agents that provide tensile strength, ensuring the material can withstand significant stress.
This combination of materials gives GRP unique properties that are valuable across various industries.
Advantages of Using GRP
1. Lightweight and High Strength
One of the most compelling benefits of GRP is its exceptional strength-to-weight ratio. This feature allows manufacturers to create products that are strong yet easy to handle and transport. As a result, companies can save on shipping costs and improve efficiency when using GRP.
2. Corrosion Resistance
GRP is inherently resistant to corrosion caused by chemicals and environmental factors. This makes it an ideal choice for applications in marine environments or for products that will be exposed to harsh chemicals.
3. Durability and Longevity
Components made from GRP are designed to last. Their resistance to wear and UV degradation means they maintain their properties and aesthetics over time, leading to lower maintenance costs and prolonged lifespans.
4. Design Flexibility
The manufacturing process of GRP allows for intricate and complex shapes that may be difficult or impossible to achieve with traditional materials. This design flexibility means it can be tailored to meet specific performance and aesthetic requirements.
Applications of GRP
1. Construction and Architecture
In the construction industry, GRP is used in:
- Roofing: GRP roofing solutions are popular due to their waterproofing capabilities and durability.
- Cladding: The use of GRP panels can enhance the aesthetics while providing insulation and weather protection.
- Structural Components: Many buildings utilize GRP for beams and supports due to its lightweight nature and strength.
2. Marine Industry
GRP is extensively utilized in the marine sector for:
- Boat Hulls: The lightweight and corrosion-resistant nature of GRP makes it ideal for constructing boat hulls.
- Decking: GRP offers slip-resistant surfaces that are essential for safety on boats.
3. Automotive Sector
With the automotive industry's constant drive towards reducing weight for fuel efficiency, GRP is increasingly utilized for:
- Body Panels: Cars made with GRP components can achieve lower weight without sacrificing strength.
- Interior Components: GRP allows for intricate design while providing durability.
4. Aerospace Applications
The aerospace industry takes advantage of GRP for:
- Aircraft Components: The materials provide strength while keeping weight down, essential for fuel efficiency.
- Interior Design: The aesthetic flexibility of GRP makes it suitable for creating luxurious interiors.
Why Choose Celtic Composites for GRP Solutions?
1. Expertise and Experience
Celtic Composites has extensive experience in the production of high-quality GRP materials. Our team of experts understands the nuances of GRP and can provide tailored solutions to meet the specific needs of various industries.
2. Custom Solutions
At Celtic Composites, we offer a range of custom solutions that cater to the specific requirements of our clients. Whether it’s a unique shape, size, or performance specification, we strive to deliver products that exceed expectations.
3. Commitment to Quality
Quality is at the forefront of our production processes. Each GRP product we manufacture undergoes rigorous quality checks to ensure it meets the highest industry standards.
4. Sustainable Practices
We are committed to sustainable manufacturing practices. Our production methodologies minimize waste and focus on using materials that have a reduced environmental impact.
The Future of GRP
The future of GRP looks promising. As technology advances, the potential applications of GRP will expand even further. Research into new resins and reinforcements will lead to improved properties of GRP materials, making them suitable for even more demanding applications.
Innovations in GRP Technology
Innovations such as smart GRP, which incorporates embedded sensors and technology, are on the horizon. These advancements will enable GRP products to provide real-time data on performance and condition, significantly enhancing maintenance strategies.
Conclusion
GRP is not just a material; it's a game-changer across various industries, from construction and automotive to aerospace and marine applications. As a leading provider, Celtic Composites is dedicated to advancing the possibilities of GRP. With its advantages of durability, lightweight characteristics, and design flexibility, the future of GRP is bright.
For industries looking to enhance their production and reduce costs while maintaining quality, investing in GRP materials from Celtic Composites is the step forward. Explore our offerings and discover how we can help you innovate and succeed in your market.