Understanding the Vital Role of Injection Molding Manufacturers
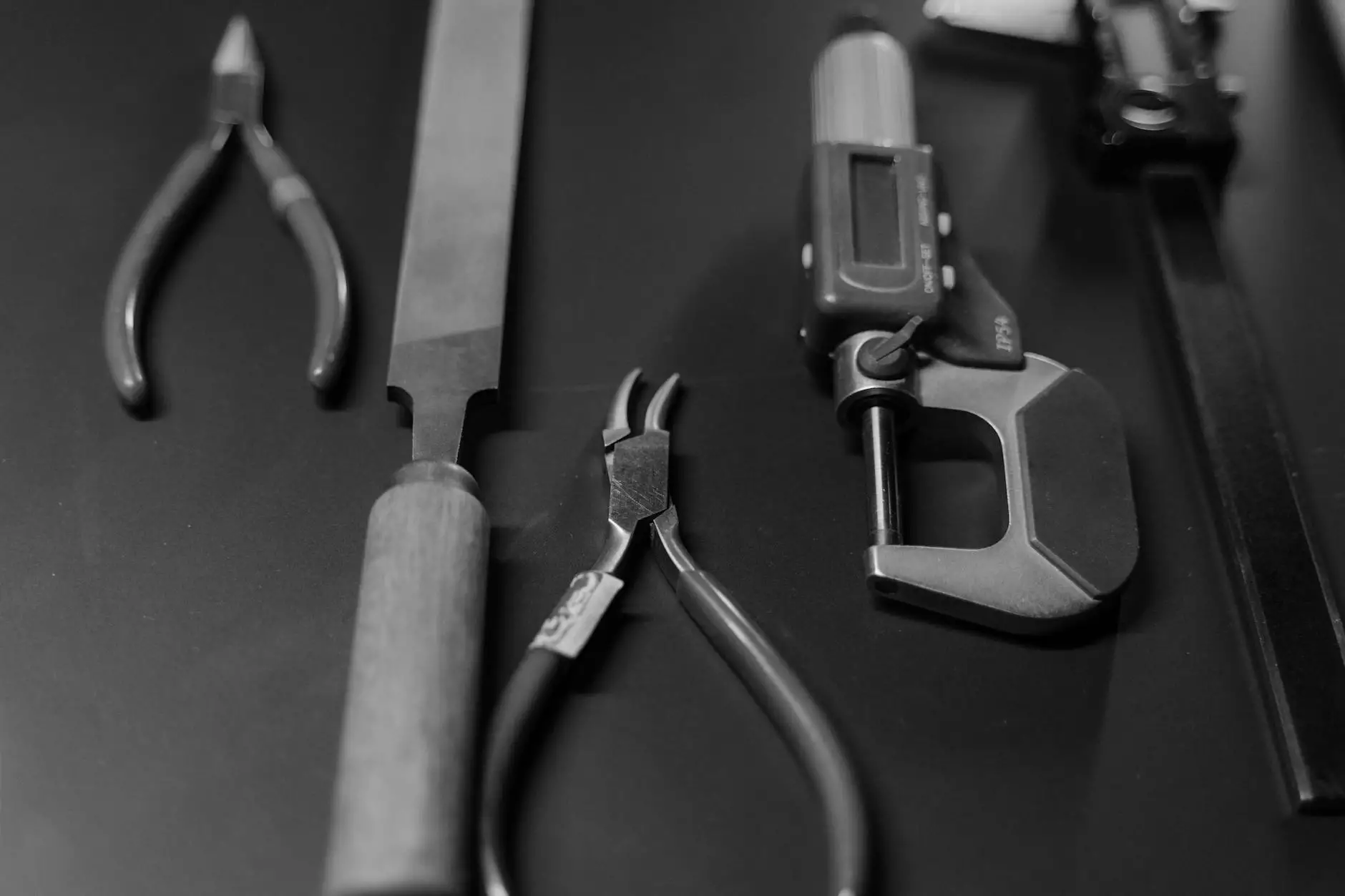
In today's fast-paced manufacturing environment, injection molding manufacturers play a crucial role in turning concepts into reality. This article explores the intricate processes, advantages, and impact of injection molding on various industries, particularly within the realm of metal fabrication.
What is Injection Molding?
Injection molding is a manufacturing process used to produce parts by injecting molten material into a mold. This process is essential for creating complex and intricate shapes that are not only durable but also cost-effective. Injection molding can be employed with various materials, including plastics, metals, and ceramics, making it versatile across numerous industries.
The Process of Injection Molding
The injection molding process can be broken down into several key stages:
- Material Selection: Choosing the right material is critical. Common materials used in injection molding include thermoplastics, thermosetting plastics, and metals.
- Melting the Material: The selected material is then heated until it reaches a molten state, suitable for injection.
- Injection into the Mold: The molten material is injected into a pre-designed mold, where it takes the shape of the desired component.
- Cooling and Solidification: The injected material cools and solidifies within the mold, forming the finished part.
- Demolding: Once solidified, the mold is opened, and the finished product is ejected.
- Finishing: The final step often involves secondary operations like trimming, painting, or surface treatment.
Benefits of Working with Injection Molding Manufacturers
Partnering with a proficient injection molding manufacturer offers numerous advantages, particularly for businesses in the metal fabrication sector:
1. Efficiency in Production
Injection molding is known for its high efficiency and speed of production. These manufacturers can create thousands of identical parts in a short period, which significantly reduces lead times for new projects.
2. Cost-Effectiveness
Once a mold is created, the cost per unit decreases dramatically with increased production volume. This economy of scale makes injection molding an attractive option for large production runs.
3. Design Flexibility
Injection molding allows for a high degree of design freedom. Complex geometries and internal features can be created without significant additional cost, which is valuable for innovation in product development.
4. Waste Reduction
Since the process utilizes almost all of the material used, waste is minimized. This is particularly important in industries where sustainability and environmental responsibility are priorities.
5. High-Quality Finished Products
Injection molding produces parts with excellent surface finishes and precise dimensions. This high level of quality is particularly essential in industries like automotive and medical, where precision is non-negotiable.
Applications of Injection Molding in Metal Fabrication
Injection molding is extensively applied in various sectors of metal fabrication:
1. Automotive Industry
The automotive industry utilizes injection molding for producing complex components such as dashboards, bumpers, and various interior parts. The ability to manufacture lightweight yet durable parts is a significant factor in automotive design.
2. Electronics
In the electronics field, injection molding is used for creating casings, housing for devices, and intricate internal parts that require high precision and reliability.
3. Medical Devices
The medical sector relies heavily on injection molding to produce components that meet strict hygiene and regulatory standards. Items like syringes, implants, and surgical tools are all produced through this process.
4. Consumer Products
From toys to kitchen utensils, consumer products benefit greatly from the efficiency and versatility of injection molding. This method allows for rapid prototyping and quick market delivery.
Choosing the Right Injection Molding Manufacturer
Choosing the right injection molding manufacturer is paramount for success in any project. Here are some critical factors to consider:
- Experience and Expertise: Look for a manufacturer with a proven track record in your industry.
- Technological Capability: Ensure they have up-to-date equipment and technologies to meet your specific needs.
- Quality Assurance: Check if they comply with quality standards such as ISO 9001.
- Customer Service: Choose a partner who communicates effectively and supports you throughout the process.
- Cost Competitiveness: Get quotes, but remember that the cheapest option may not always provide the best value.
Innovations in Injection Molding
The world of injection molding is ever-evolving, with advancements continuously shaping the way manufacturers operate. Key innovations include:
1. Advanced Materials
New materials being developed offer improved properties, such as greater strength, flexibility, and resistance to environmental factors. Manufacturers are adopting these materials to enhance product performance.
2. Automation and Robotics
The integration of robotics in injection molding processes leads to increased precision and reduced cycle times. Automated systems can handle tasks from material loading to quality inspection, allowing for seamless operations.
3. Sustainable Practices
With a growing emphasis on sustainability, many manufacturers are adopting eco-friendly practices such as using recycled materials and reducing energy consumption in their operations.
Final Thoughts on the Impact of Injection Molding Manufacturers
In conclusion, the importance of injection molding manufacturers in today's manufacturing landscape cannot be overstated. Their ability to provide efficient, cost-effective solutions while maintaining high-quality standards makes them invaluable partners in various industries. Businesses looking to innovate their product lines or enhance their manufacturing processes should explore the multifaceted advantages offered by injection molding.
As the demand for faster, more efficient, and sustainable manufacturing practices increases, companies like Deep Mould, an esteemed name among injection molding manufacturers, continue to lead the charge in the metal fabrication sector, ensuring that they not only meet current demands but also anticipate future needs.