CNC Lathe Machining Parts Suppliers: Enhancing Precision and Quality in Metal Fabrication
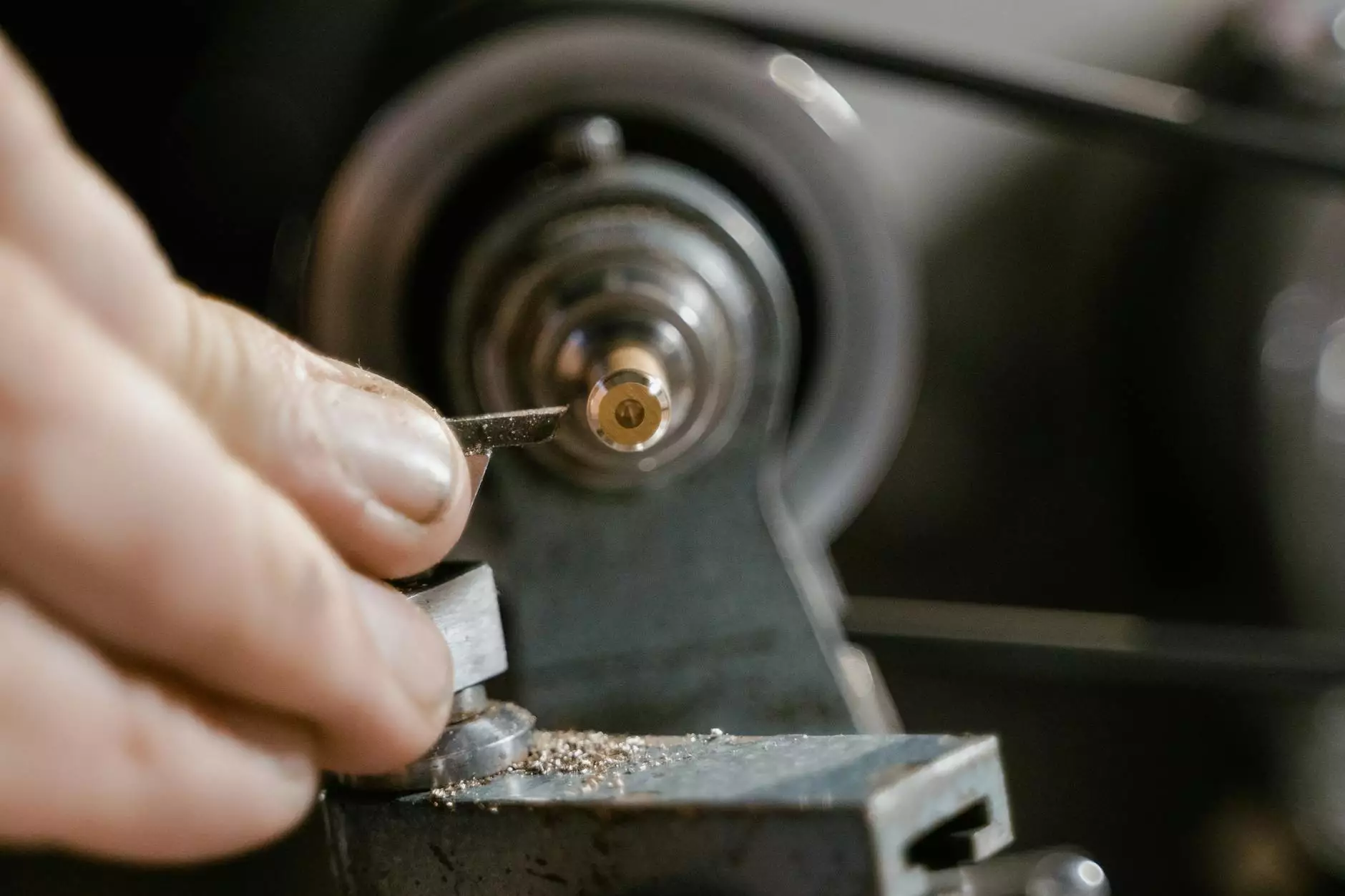
CNC lathe machining is a critical process in today's manufacturing landscape, playing a pivotal role in the production of high-quality components. When businesses require precision-engineered parts, the expertise and capabilities of cnc lathe machining parts suppliers become indispensable. In this article, we delve into the world of CNC machining, exploring its benefits, the criteria for selecting a supplier, and how these suppliers can transform your operations.
Understanding CNC Lathe Machining
CNC (Computer Numerical Control) lathe machining is a manufacturing process that utilizes computerized controls to cut and shape materials, mainly metals, with incredible accuracy. This process is particularly advantageous for producing cylindrical components such as rods, shafts, and fittings, which are common in various industries including automotive, aerospace, and construction.
- Increased Precision: CNC machines can achieve tolerances of +/-0.001 inches or better.
- Consistency: Once programmed, CNC lathes produce identical parts repetitively without variation.
- Efficiency: CNC lathes can operate continuously, reducing production time significantly.
- Flexibility: They can be reprogrammed to manufacture different parts, making them versatile for changing needs.
Why Partner with CNC Lathe Machining Parts Suppliers?
Selecting the right cnc lathe machining parts suppliers can profoundly impact your production capability. Here are several compelling reasons to engage with knowledgeable suppliers:
1. Access to Expertise and Advanced Technology
CNC lathe machining parts suppliers invest heavily in the latest technologies and have a team of skilled engineers and machinists. This expertise ensures that they can handle complex designs and adapt to your specific needs. Leveraging their experience can lead to better design solutions and manufacturing processes.
2. Cost-Effective Solutions
By outsourcing your machining needs to reputable suppliers, you can reduce overhead costs associated with labor, machinery, and maintenance. Furthermore, suppliers often benefit from bulk purchasing, leading to lower material costs that can be passed on to you.
3. Quality Assurance
Quality control is paramount in manufacturing. Established cnc lathe machining parts suppliers implement rigorous inspection processes to ensure that all machined parts meet the highest standards. This includes using tools such as Coordinate Measuring Machines (CMM) and laser scanners for precision measurement.
Choosing the Right CNC Lathe Machining Parts Supplier
Not all cnc lathe machining parts suppliers are created equal. To ensure a fruitful partnership, consider the following criteria:
1. Experience and Reputation
Look for suppliers with a proven track record in the industry. A supplier’s experience can often be gauged through case studies, client testimonials, and years in business. The reputation in the market can provide insight into reliability and service quality.
2. Range of Services Offered
A comprehensive supplier should provide various services beyond basic machining. These can include:
- Prototyping and design assistance
- Material selection support
- Assembly and finishing services
- Rapid manufacturing to accommodate urgent needs
3. Technology and Equipment
Evaluate the technology and equipment that the supplier uses. High-quality, modern CNC lathes and ancillary equipment significantly impact the quality and efficiency of the machining process.
4. Customer Service and Support
A good relationship with your supplier is essential. Choose suppliers who offer exceptional customer service and are willing to communicate openly about timelines, production updates, and potential issues.
Industries that Benefit from CNC Lathe Machining
The versatility of CNC lathe machining makes it invaluable across various sectors, including:
Aerospace Industry
In aerospace, precision is non-negotiable. Components like turbine blades and structural parts must adhere to stringent safety and quality standards. CNC lathe machining allows manufacturers to produce these components with utmost accuracy.
Automotive Sector
The automotive industry relies heavily on CNC machining for parts such as axle shafts, engine blocks, and transmission components. Suppliers play a crucial role in providing these critical components efficiently and reliably.
Medical Devices
Medical device manufacturing requires parts that meet strict regulatory standards. CNC lathe machining allows for producing intricate components that are used in surgical instruments and implants.
Tool and Die Making
The manufacture of tooling systems and dies for production lines often employs CNC lathe machining due to its capacity for detail and precision, ensuring the final products function effectively.
Process of CNC Lathe Machining
Understanding the CNC lathe machining process can clarify its value and efficiency:
1. Design Phase
The process typically starts with a detailed design phase, where engineers use CAD (Computer-Aided Design) software to create the parts' specifications.
2. Programming
Once the design is finalized, the next step involves programming the CNC lathe with G-code, which directs the machine’s movements and operations.
3. Machining
The machining phase entails loading the raw material into the CNC lathe, where it is cut, shaped, and finished per the design specifications. The automated process ensures precision and repeatability.
4. Quality Control
After machining, parts undergo quality inspections, including dimensional checks and surface finish evaluations to ensure they meet client specifications.
5. Delivery
Finally, the finished products are packaged and delivered to the client, ready for installation or further processing.
Future Trends in CNC Lathe Machining
The machining industry is always evolving. Key trends that cnc lathe machining parts suppliers must watch include:
1. Automation and Smart Manufacturing
The integration of IoT (Internet of Things) in CNC machines allows for more automated operations, real-time monitoring, and predictive maintenance, which can reduce downtime and increase efficiency.
2. Increased Use of Advanced Materials
As industries push the boundaries of technology, the demand for CNC machining of advanced materials like titanium and composite materials is on the rise, necessitating suppliers to adapt their skills and equipment accordingly.
3. Sustainability in Manufacturing
With sustainability becoming more important, suppliers are seeking ways to reduce waste and improve energy efficiency in their machining processes, which can lead to more eco-friendly operations.
The Importance of Communication with Suppliers
Establishing strong lines of communication with your cnc lathe machining parts suppliers fosters a productive partnership. Regular updates and feedback can help troubleshoot issues quickly and improve overall satisfaction.
1. Regular Progress Updates
Frequent communication about ongoing projects ensures that timelines are met and expectations are aligned. This feedback loop can be instrumental in enhancing clarity and reducing misunderstandings.
2. Addressing Challenges
Open dialogue allows both parties to collaborate more effectively on any challenges encountered during the machining processes. Addressing these issues proactively can result in faster resolutions.
Conclusion: Empowering Your Business with CNC Lathe Machining Parts Suppliers
Engaging with high-quality cnc lathe machining parts suppliers presents an incredible opportunity to enhance your manufacturing capabilities. With their expertise, access to advanced technology, and commitment to quality, your business can stay competitive in an ever-changing landscape.
For businesses in various sectors, choosing the right CNC lathe machining partner can be the key to unlocking increased efficiency, lower costs, and superior product quality. By focusing on the factors that matter most—experience, technology, customer support, and scalability—you can forge a partnership that will drive success for years to come.